Achieving Unprecedented Accuracy in Assembling Workpieces Over 100 Meters in Length with Radian Laser Tracker.
In the realm of industrial production, the assembly of extra-large workpieces poses significant challenges. These workpieces, characterized by their massive volume and weight, demand strict manufacturing and assembly tolerances. Traditional methods often fall short in ensuring the required precision. But API’s Radian Laser Tracker series provides a simple 3-step measurement plan that results in:
· Enhanced Accuracy: Achieved an overall assembly accuracy within a remarkable 0.2mm for workpieces over 100 meters.
· Time Efficiency: Streamlined the measurement process, significantly reducing assembly time.
· Cost Savings: Minimized material wastage and rework, leading to tangible cost savings.
· Unified Measurement Standard: Ensured consistent accuracy standards across all assembly points, irrespective of their position.
Extra-large workpieces are integral to certain industrial production sectors. The traditional ways of assembly often struggle to ensure the overall precision due to the sheer size and weight of these workpieces.
The Challenge: Laser Tracker Distance
Ensuring the overall assembly accuracy of workpieces that span over 100 meters in length, with a maximum allowable error margin of just 0.3mm.
API’s Solution: Radian Laser Tracker PLUS
API’s Radian Laser Tracker offers a solution tailored for such challenges. The Radian Plus is Capable of large-size and high-precision 3D measurements, the laser tracker can measure across tens of meters with micron-level accuracy. The tracker’s flexibility allows operators to easily collect spatial coordinates, enabling precise analysis of position tolerances.
Implementation:
1. Setting Up Tracker Stations: Based on the workpiece’s characteristics, multiple laser tracker stations are strategically positioned to ensure optimal coverage.
2. Data Collection: Each station measures all visible points, forming a comprehensive data network.
3. Measurement Adjustment & Assembly: Post data collection, software is used to bundle all data for adjustment analysis. The dominant station’s data is given higher weightage to derive a unified accuracy standard.
Results:
The implementation of the Radian Laser Tracker ensured that the overall assembly accuracy of the workpiece, spanning over 100 meters, was maintained within a remarkable 0.2mm, surpassing the set tolerance requirements.
API’s Radian Laser Tracker has proven to be an invaluable tool in the realm of industrial production, especially when precision is paramount. This case stands as a testament to API’s commitment to
innovation and accuracy, ensuring that even the most challenging assembly requirements are met with unparalleled precision.
相关新闻:
High Precision Assembly of Extra-Large Workpiece with API Radian Laser Tracker
Achieving Unprecedented Accuracy in Assembling Workpieces Over 100 Meters in Len
Radian Laser Tracker Application 100 Meters Workpiece High Precision Alignment Assembly
High Precision Assembly of Extra Large Workpiece In some fields of industrial pr
API Helps ŠKODA Auto Volkswagen India Install, Level Robotic Welding Lines
MSP Follows 4-Step Process to Ensure Accuracy from InstallationVolkswagen’s main
Case Study: Durr Schneck Rotec – India
API, Durr Schenck Provide High Precision Wheel Alignment for Commercial Vehicles
Learn More:
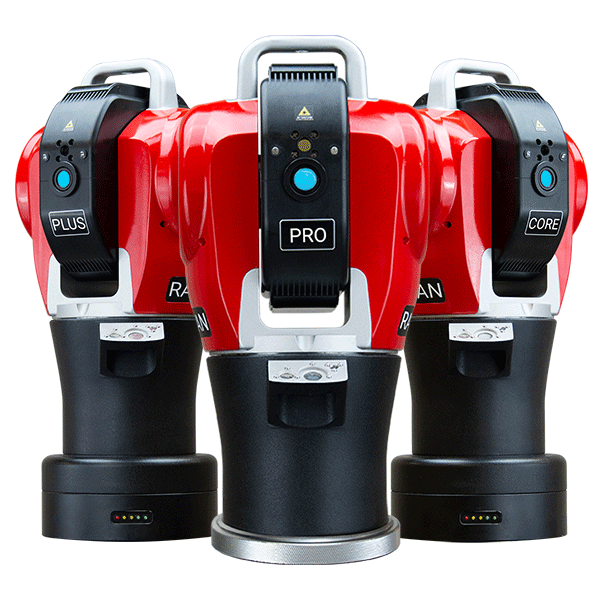
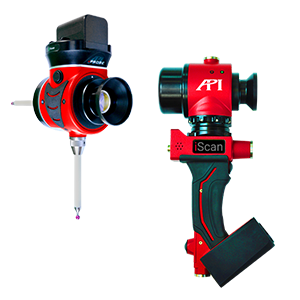
激光跟踪仪靶球&测头
Maximize laser tracker productivity with hand held and 激光跟踪仪主动靶标.
Learn More /laser-tracker-targets
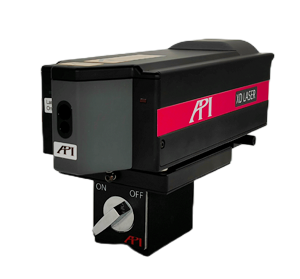
XD Laser CMM Calibration
The XD Laser is the only assessment system that can measure all 6 error parameters simultaneously in a single set-up
Learn More /xd-laser
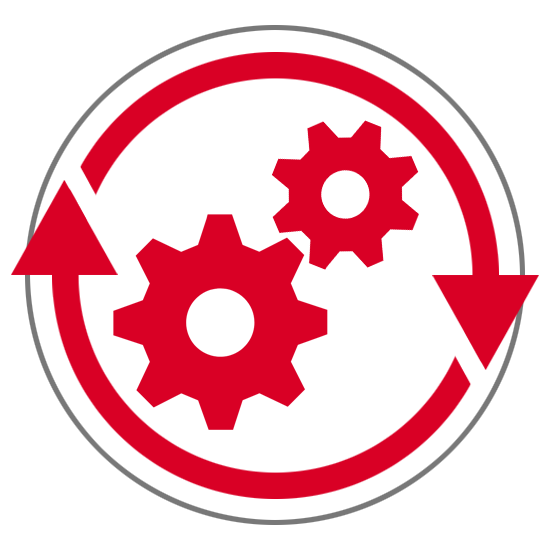
API Reverse Engineering Service
Reverse engineering services include scan as-built parts to creation of a 3D digital point cloud and CAD Model.
Learn More /reverse-engineering/