High Precision Assembly of Extra Large Workpiece
In some fields of industrial production, the use of extra large workpiece is involved. Extra large workpiece often has the characteristics of huge volume and huge weight, and based on the requirements of production for quality, the manufacturing and assembly tolerance of the workpiece are strictly limited, so the overall assembly accuracy of the workpiece is difficult to ensure by using the traditional way.
According to the production practice, it is the most efficient, effective and economic benefit way to use laser tracker to inspect the precision of the workpiece with large volume and weight and strict assembly tolerance requirements.
Laser Tracker can be used for large-size and high-precision 3D measurement. The measurement radius can often reach tens of meters. The space measurement accuracy is in micron level (μm, 1/1000mm), and the use is relatively flexible. The operator only need to take the SMR (laser tracker target ball) to contact the measurement points, the laser tracker will shoot laser to the center of the target ball (SMR) and lock, track and read the spatial coordinates of the contact position points and record them in the software. Through the spatial coordinates of these collected points, various lines, planes and bodies can be constructed, so as to accurately analyze the position tolerances and achieve the effect of measurement and inspection.
Figure 1: API Radian Series Laser Trackers
Laser Tracker Measures Extra Large Workpiece - Points to Note
Although the laser tracker is with high accuracy and wide measuring range, there are still some points worth paying attention to and summarizing in the assembly of some extra large workpiece of tens of meters and more than 100 meters, so as to give better play to the characteristics of the laser tracker and further improve the assembly accuracy and quality:
(1) Unified Standard of Global Accuracy
Although normally the assembly accuracy standard can be achieved within the effective working range of the laser tracker, the phenomenon that the measurement accuracy of the near-end is higher than that of the far-end is objectively existed based on the working principle and characteristics of the laser tracker itself.
This phenomenon is caused by the angle error of laser tracker. Under the same angle deviation, the measurement uncertainty in the far-end will be much larger than its near-end measurement uncertainty.
Figure 2: Diagram of Angle Error of Laser Tracker
As shown in Figure 2, when the laser tracker measures the near-end plane P1 and the far-end plane P2, the projection points of the laser on the plane should theoretically be center A and center B respectively. However, because of the angle error α of the laser tracker, the laser may be projected at any point within the area of circle C and circle F. In the area range of circle C and circle F, that is, the measurement uncertainty of near-end plane P1 and far-end plane P2 measured by the tracker respectively; As observed from the front view at the lower right corner, the area of circle F is much larger than that of circle C, that is, the measurement uncertainty range at the far-end is much larger than that at the near-end.
In production, the assembly accuracy requirement of the whole workpiece is unified; Therefore, when a single laser tracker is used to assemble an extra large workpiece, even though its near-end and far-end precision can meet the requirements under normal circumstances, the assembly points in different positions or sections will still be in different accuracy standards; If it is necessary to keep improving, further improve the assembly accuracy, and make each section of the workpiece under the same accuracy standard, it is necessary to control the error range at the far-end of a single tracker.
(2) The Relationship between Stations
When measuring the workpiece beyond the measuring range of the laser tracker or measuring the shielding surface of the workpiece, it is often necessary to move the laser tracker to another position to obtain sufficient measuring coverage, namely: "tracker location" or "tracker station transfer".
Figure 3: Diagram of "Tracker Location"
As shown in Figure 3, when doing tracker location operation, "location points" (usually 4 points) should be set at the positions that can be observed at both stations, and these "location points" should be measured at both stations by laser tracker respectively. Then, the "best-fit" function of the software is used to bring the two stations into the same coordinate system for measurement.
Using the method of "tracker location" + "best-fit" to carry out the measurement has the advantage of being relatively fast. It can realize the full coverage of the measuring range of conventional size workpiece by moving 1-2 stations, and meet the requirements of measuring accuracy at the same time.
However, when assembling extra large workpiece, if the "tracker location" + "best-fit" method is used, each new station will accumulate the errors of each station in front, that is, the more stations are set, the greater the measurement error, and continue to cause the inconsistency of accuracy standards of each assembly point.
It can be seen that the assembly of extra large workpiece also has strict requirements for the error of the relationship between tracker stations.
API Solution on Extra Large Workpiece High Precision Alignment Assembly
Through practical demonstration, the case introduced in the following text as a reference, the method of "adjustment measurement" by laser tracker can be used to meet the requirements of users for ultra-high precision performance of extra large workpiece assembly.
Figure 4: Diagram of Structure and Size of The Extra Large Workpiece in This Case
Application Case Study: High Precision Alignment Assembly of Extra Large Workpiece with a Cumulative Length of Over 100 Meters.
Workpiece characteristics & measurement requirements: As shown in Figure 4, the cumulative length of each section of the workpiece to be measured exceeds 100 meters; The maximum allowable error of assembly is 0.3mm.
Instrument selection: according to the requirements of the measurement and the characteristics of the workpiece, the API Radian Pro laser tracker is selected as the equipment to perform the operation. Radian Pro laser tracker integrated with IFM laser, its distance measuring accuracy meets 1/10000mm level, higher than the laser tracker space accuracy (1/1000mm level).
Figure 5: Diagram of Adjustment Measurement Station Setting and Data Collection of Laser Tracker
Measurement Steps & Key Points
Step 1: Set Up Tracker Stations Based on Workpiece Characteristics
According to the characteristics of the workpiece, several laser tracker stations are set up in the most suitable position to form a high quality coverage of the measuring range of the workpiece. When setting up the stations, it is necessary to consider the advantages of the near-end precision of the laser tracker mentioned above and the distance measuring advantages of the IFM laser tracker, and set the tracker position within the best measurement range of the frontal workpiece as far as possible (see Figure 5).
Step 2: Data Collection
As shown in Figure 5, the tracker at each station measures all points to be measured within the visual range to form a data network, which is comprehensively recorded in the software for final measurement adjustment analysis.
Step 3: Measurement Adjustment Data Analysis and Alignment Assembly
When data collection is completed, it can be set in the software to bundle all data for adjustment analysis, and take the data collected by the tracker at the dominant station as a higher weight to obtain the final overall measurement result under the unified accuracy standard and unified coordinate system.
Conclusion
This case verifies that the overall assembly accuracy of the workpiece with a total length of more than 100 meters is controlled within 0.2mm, which fully meets the tolerance requirements.
相关新闻:
Application of Radian laser tracker in the field of measurement and calibration of papermaking Machi
BackgroundA large paper enterprise decided to carry out systematic accuracy cali
Application of Radian laser tracker in the field of inspection of large box Parts_api Measuring inst
A high-tech enterprise in Suzhou has been supplying all kinds of large box parts
Precision inspection and performance evaluation SOLUTIONS_API Measuring Instrument Co., Ltd. for CNC
About the rapid detection of CNC machine tools The cost of time is of great sign
Three-dimensional dynamic detection of simulation PLATFORM_API measuring instrument Company
Simulation platform & 3D dynamic measurement For the manufacturing and research
Learn More:
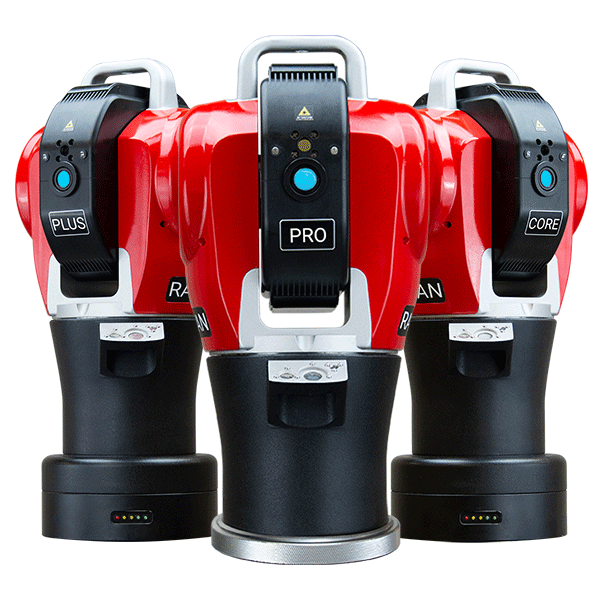
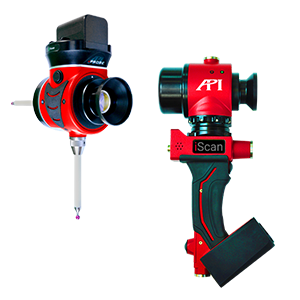
激光跟踪仪靶球&测头
Maximize laser tracker productivity with hand held and 激光跟踪仪主动靶标.
Learn More /laser-tracker-targets
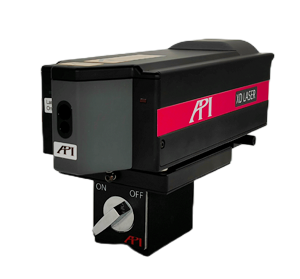
XD Laser CMM Calibration
The XD Laser is the only assessment system that can measure all 6 error parameters simultaneously in a single set-up
Learn More /xd-laser
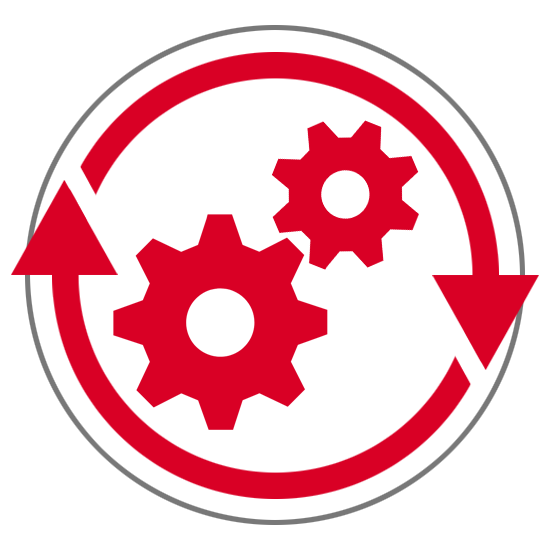
API Reverse Engineering Service
Reverse engineering services include scan as-built parts to creation of a 3D digital point cloud and CAD Model.
Learn More /reverse-engineering/